[ Huaqiang Security Network News ] 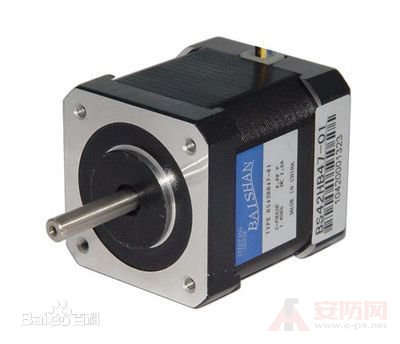
Before introducing the working principle of the stepping motor, we introduce the concept of the stepping motor. The stepping motor converts the electric pulse signal into an angular displacement to control the rotation of the micro-motor. Acting as an actuator in the automatic control unit. Each time a pulse signal is input, the stepping motor is further advanced, so it is also called a pulse motor. Stepper motors are mostly used in external devices for digital computers, as well as devices such as printers, plotters, and disks.
The driving power of the stepping motor is composed of a variable frequency pulse signal source, a pulse distributor and a pulse amplifier, whereby the driving power source supplies a pulse current to the motor winding. The running performance of the stepper motor is determined by the good fit between the motor and the drive power.
The advantage of stepping motor is that there is no accumulated error, the structure is simple, the use and maintenance are convenient, the manufacturing cost is low, the stepping motor has the ability to drive the load inertia, and is suitable for small and medium-sized machine tools and places where the speed precision is not high. The disadvantage is that the efficiency is low. It is very hot and sometimes "out of step".
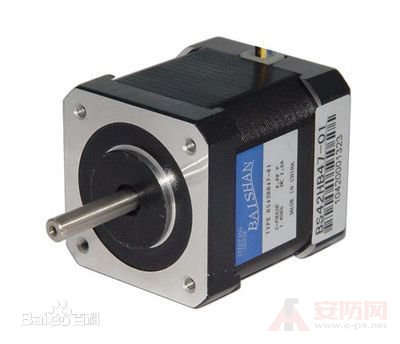
Stepper motor working principle
A stepper motor is an open-loop control element that converts an electrical pulse signal into an angular displacement or a linear displacement. In the case of non-overloading, the speed and stop position of the motor depend only on the frequency of the pulse signal and the number of pulses, and are not affected by the load change, that is, a pulse signal is applied to the motor, and the motor rotates through a step angle. The existence of this linear relationship, coupled with the stepper motor only periodic error without cumulative error. It is very simple to control the change with a stepping motor in the control field such as speed and position.
Although stepper motors have been widely used, stepper motors are not as conventional DC motors, and AC motors are used under normal conditions. It must be composed of a dual ring pulse signal, a power drive circuit, etc. to form a control system. Therefore, the use of stepper motors is not an easy task. It involves many professional knowledge such as machinery, motors, electronics and computers.
Nowadays, there are many manufacturers that produce stepping motors, but they have professional technicians who can develop them themselves. There are very few manufacturers. Most of them are only one or twenty people, even the most basic equipment. Just in a blind copying stage. This causes the user to cause a lot of trouble in product selection and use. In view of the above, we decided to take a wide range of inductive stepper motors as an example. Describe the basic working principle. Hope can help the majority of users in the selection, use, and machine improvement.
Reactive stepper motor working principle
The working principle of the reactive stepping motor is relatively simple. The principle of a three-phase reactive stepping motor will be described below.
1. Structure: The rotor of the motor is evenly distributed with many small teeth. The stator teeth have three excitation windings, and their geometric axes are respectively shifted from the rotor tooth axis. 0, 1/3 ã¦, 2/3 ã¦, (the distance between the axes of the adjacent two rotor teeth is the pitch of the tooth), that is, A is aligned with the tooth 1, and B and the tooth 2 are 1/3 turn to the right. C and tooth 3 are shifted to the right by 2/3ã¦, A' is aligned with tooth 5 (A' is A, tooth 5 is tooth 1). Below is the unfolded view of the fixed rotor:
2. Rotation: If phase A is energized and B and C phases are not energized, the teeth 1 are aligned with A due to the magnetic field. (The rotor is not subject to any force and is equal). If phase B is energized, when phase A and phase C are not energized, tooth 2 should be aligned with B. At this time, the rotor is shifted to the right by 1/3ã¦, at which time the teeth 3 and C are offset by 1/3ã¦, and teeth 4 and A are Offset (ã¦-1/3ã¦)=2/3ã¦. If the C phase is energized, the A and B phases are not energized, and the tooth 3 should be aligned with C. At this time, the rotor is shifted to the right by 1/3 ã¦, and the tooth 4 is aligned with the A offset by 1/3 æ¤æ—¶. If the A phase is energized, the B and C phases are not energized, the teeth 4 are aligned with A, and the rotor is shifted to the right by 1/3 㦠so that the A, B, C, and A are respectively energized, and the teeth 4 (ie, the first tooth of the tooth 1) Move to phase A, the motor rotor turns to the right by a pitch. If the A, B, C, A... is continuously energized, the motor rotates 1/3 turn per step (per pulse) and rotates to the right. If A, C, B, A... is energized, the motor will reverse. It can be seen that the position and speed of the motor are in a one-to-one correspondence between the number of times of conduction (number of pulses) and the frequency. The direction is determined by the order of conduction. However, due to the consideration of torque, stability, noise and angle reduction. The conductive state of A-AB-B-BC-C-CA-A is often used, so that 1/3 æ¯ of each step is changed to 1/6 ã¦. Even with a different combination of two-phase currents, the 1/3 turns become 1/12 ã¦, 1/24 ã¦, which is the basic theoretical basis for the motor subdivision drive. It is not difficult to introduce: there is m-phase excitation winding on the stator of the motor, and its axis is offset from the rotor tooth axis by 1/m, 2/m...(m-1)/m,1 respectively. And the conduction of the motor in a certain phase sequence can be controlled by forward and reverse - this is the physical condition of rotation. As long as this condition is met, we can theoretically manufacture stepper motors of any phase. For cost and other considerations, the market generally has two, three, four, and five phases.
3. Torque: Once the motor is energized, a magnetic field (magnetic flux Ф) will be generated between the stator and rotor. When the rotor and the stator are offset by a certain angle, the force F is proportional to (dФ/dθ). The magnetic flux Ф=Br*S Br is magnetically dense. S is the magnetic permeability area F and L*D*Br is proportional to L is the effective length of the iron core, D is the rotor diameter Br=N·I/RN·I is the excitation winding ampere number (current multiplied by the number of turns) R is magnetic Resistance. Torque = force * radius torque and motor effective volume * amperage * magnetic density is proportional (only consider linear state) Therefore, the larger the effective volume of the motor, the larger the number of excitation amps, the smaller the air gap between the stator and rotor, the motor torque The bigger, and vice versa.
Inductive stepper motor works
1. Features: Compared with the traditional reaction type, the induction rotor is equipped with permanent magnets to provide the working point of the soft magnetic material, while the stator excitation only needs to provide the changing magnetic field without having to provide the working point of the magnetic material. Therefore, the motor has high efficiency, low current and low heat generation. Due to the existence of permanent magnets, the motor has a strong back EMF, and its own damping effect is better, which makes it relatively stable during operation, low noise, and low frequency vibration. The sensor can be seen to some extent as a low-speed synchronous motor. A four-phase motor can be operated in four phases or in two phases. (Bipolar voltage drive must be used), while reactive motors cannot. For example: four-phase, eight-phase operation (A-AB-B-BC-C-CD-D-DA-A) can be used in two-phase eight-shot operation. It is not difficult to find that the condition is C=, D=. The internal winding of the two-phase motor is exactly the same as the four-phase motor. The low-power motor is usually directly connected to two-phase, and the motor with larger power is used to flexibly change the dynamic characteristics of the motor for convenient use. (Four-phase), when used in this way, it can be used as a four-phase motor, and can be used as a two-phase motor winding in series or in parallel.
2, classification
Inductive sub-motors can be divided into two phases: two-phase motor, three-phase motor, four-phase motor, five-phase motor, and so on. The frame number (motor outer diameter) can be divided into: 42BYG (BYG is the induction stepper motor code), 57BYG, 86BYG, 110BYG, (international standard), and like 70BYG, 90BYG, 130BYG are domestic standards.
3. Static index of stepper motor Terminus number: The number of pairs of excitation coils that generate different pairs of N and S magnetic fields. Commonly used m. Number of beats: The number of pulses required to complete a periodic change of the magnetic field or the conductive state is represented by n, or the number of pulses required for the motor to rotate through a pitch angle. Taking a four-phase motor as an example, there is a four-phase four-shot operation mode, that is, AB. -BC-CD-DA-AB, four-phase eight-beat operation mode is A-AB-B-BC-C-CD-D-DA-A. Step angle: corresponding to a pulse signal, the angular displacement of the motor rotor Expressed by θ. θ = 360 degrees (number of rotor teeth J * running beats), taking the conventional two-phase, four-phase, rotor teeth as a 50-tooth motor as an example. The four-shot running step angle is θ=360°/(50*4)=1.8 degrees (commonly known as the whole step), and the eight-shot running step angle is θ=360 degrees/(50*8)=0.9 degrees (commonly known as Half step). Positioning torque: The locking torque of the motor rotor itself (caused by the harmonics of the magnetic field tooth shape and mechanical error) when the motor is not energized. Static torque: When the motor is under the action of rated static electricity, the motor does not rotate, the motor The locking torque of the shaft. This torque is a measure of the motor's volume (geometry) and is independent of the drive voltage and drive power. Although the static torque is proportional to the number of electromagnetic excitation amps and the air gap between the fixed tooth rotors, it is not advisable to reduce the air gap excessively and increase the static ampere to increase the static torque, which will cause the motor to heat up. And mechanical noise.
Commercial lighting originates from the birth of public commercial spaces, creating lighting systems for commercial use in order to serve the needs of commercial lighting.Application scenarios include entertainment venues, bars, cafes, museums, cinemas, stages, hotels, hotels, conference rooms, exhibitions
Led Floodlight,Led Linear Light,Led High Bay,Commercial Led Light
Guangzhou ZG Scaffolding.co.Ltd , https://www.zgscaffolding.com